Benefits of Hangar Epoxy Flooring
Hangar epoxy flooring offers several benefits for aircraft hangars and other aviation facilities.
1. Durability: One of the primary advantages of hangar epoxy flooring is its exceptional durability. This type of flooring is designed to withstand heavy equipment, constant foot traffic, and the weight of aircraft. It can resist damage from impact, abrasion, and chemicals, making it ideal for hangar environments where there is a high level of activity.
2. Safety: Hangar epoxy flooring is known for its excellent slip resistance, providing a safe surface for workers and pilots. It can be customized with anti-slip additives to enhance its grip and reduce the risk of accidents. Additionally, this type of flooring is resistant to fire and can help prevent the spread of flames, enhancing the overall safety of the hangar.
3. Easy Maintenance: Hangar epoxy flooring is incredibly easy to clean and maintain. It creates a seamless surface that is resistant to stains, dust, and dirt, allowing for quick and effortless cleaning. Regular sweeping and occasional mopping are usually sufficient to keep the floor looking pristine. This easy maintenance saves time and effort for hangar staff.
4. Chemical Resistance: Aviation facilities often deal with spills and leaks of various chemicals, such as fuel and hydraulic fluids. Hangar epoxy flooring is highly resistant to these substances, ensuring that they do not penetrate the surface or cause long-term damage. This chemical resistance also makes the flooring easy to clean, as spills can be wiped away without leaving stains or marks.
5. Aesthetics: Hangar epoxy flooring is available in a wide range of colors and finishes, allowing hangar owners to choose a design that suits their preference and complements their branding. The glossy finish of epoxy flooring can enhance the overall appearance of the hangar, creating a professional and polished look.
6. Cost-effective: Despite its numerous advantages, hangar epoxy flooring is a cost-effective option in the long run. Its durability and low maintenance requirements reduce the need for frequent repairs and replacements, saving money over time. Additionally, the extended lifespan of epoxy flooring means that hangar owners do not have to invest in floor renovations frequently.
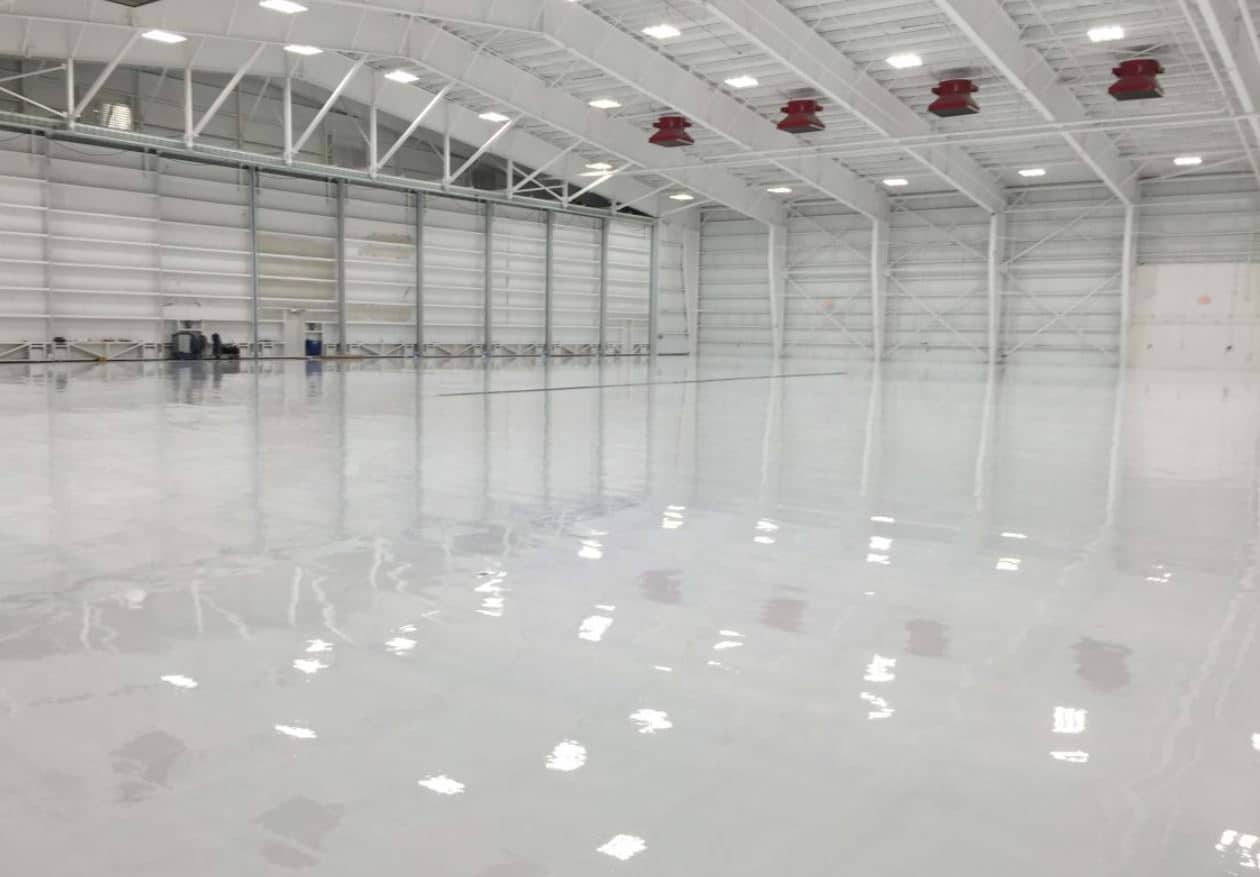
Installation Process of Hangar Epoxy Flooring
Preparation:
1. Clear the hangar floor of any existing coatings, dirt, or debris. Use a floor grinder or shot blaster to remove any previous coatings or roughen the surface for better adhesion.
2. Repair any cracks, holes, or damaged areas in the concrete floor using an epoxy patching compound. Allow the compound to cure according to the manufacturer’s instructions.
3. Thoroughly clean the floor using a degreaser and a scrub brush to remove any oil, grease, or other contaminants. Rinse the floor with clean water and allow it to dry completely.
Priming:
1. Apply a primer coat to the prepared concrete surface using a roller or brush. The primer helps to improve adhesion and prevent air bubbles from forming during the application of the epoxy coating. Follow the manufacturer’s instructions for mixing and applying the primer.
2. Allow the primer to dry for the recommended time, typically 8-12 hours, or as specified by the manufacturer.
Epoxy Coating Application:
1. Mix the epoxy coating according to the manufacturer’s instructions. Use a mixing paddle and a drill to achieve a thorough and homogenous mixture.
2. Start applying the epoxy coating along the edges of the hangar floor using a brush or an edging tool. Make sure to coat the floor-to-wall junctures and corners.
3. Use a roller or a squeegee to apply the epoxy coating in larger sections of the hangar floor. Work in small manageable areas to ensure even coverage and avoid the epoxy drying before it can be spread.
4. Spread the epoxy coating evenly across the floor, following the manufacturer’s recommended thickness. Use a back-rolling technique to remove any excess epoxy and create a smooth and uniform finish.
5. If desired, add decorative flakes or chips to the wet epoxy coating for added texture and aesthetics. Sprinkle the flakes evenly across the floor and allow the epoxy to cure as specified by the manufacturer.
6. Apply a second coat of epoxy, following the same application process as the first coat. This second coat helps to further strengthen and protect the hangar floor.
7. Allow the epoxy coating to cure for the recommended time, usually 24-48 hours, or as specified by the manufacturer. Avoid foot traffic or any heavy equipment on the floor until it is fully cured.
Maintenance Tips for Hangar Epoxy Flooring
Proper maintenance of hangar epoxy flooring is essential to ensure its longevity and performance. Here are some maintenance tips to keep your hangar epoxy flooring in top condition:
Regular Cleaning:
Regular cleaning is crucial to remove any dirt, debris, and spills that may accumulate on the epoxy flooring. Use a soft-bristle broom or a dust mop to sweep the floor daily to prevent any abrasive particles from scratching the surface. For more thorough cleaning, use a mild detergent or a specialized epoxy cleaner diluted in water. Avoid using harsh chemicals or abrasive cleaners as they can damage the epoxy coating.
Prompt Spill Cleanup:
Accidental spills of chemicals, oils, or fuels can occur in hangar environments. It is important to promptly clean up any spills to prevent them from seeping into the epoxy flooring and causing stains or damage. Use an absorbent material, such as a cloth or paper towel, to blot and remove the spill. Rinse the area with water and mild detergent if necessary, and ensure it is completely dry before resuming normal activities.
Protect Against Heavy Loads:
Hangar epoxy flooring is designed to withstand heavy loads, but it is still important to take precautions to prevent any potential damage. Use floor protectors, such as mats or rubber pads, under heavy equipment or machinery to distribute the weight and prevent indentation or scratching. Be cautious while moving heavy objects to avoid dragging or sliding them across the floor, as this can cause abrasion or gouging.
Regular Inspections:
Perform regular inspections of your hangar epoxy flooring to identify any signs of wear, damage, or deterioration. Look for areas where the epoxy coating may be peeling, chipping, or cracking. If any damage is detected, it is important to address it promptly to prevent further deterioration. Depending on the severity of the damage, you may need to consult a professional epoxy flooring contractor for repairs or touch-ups.
Avoid Excessive Moisture:
While epoxy flooring is resistant to moisture, excessive exposure to water or liquids can still cause problems over time. Avoid leaving standing water on the floor for long periods and wipe up any spills or moisture promptly. Ensure that any drainage systems in the hangar are functioning properly to prevent water accumulation. If necessary, consider using epoxy floor coatings with additional moisture barrier properties for areas prone to high moisture levels.
Choosing the Right Hangar Epoxy Flooring Contractor
When it comes to installing epoxy flooring in your hangar, choosing the right contractor is crucial. The quality of the installation can have a significant impact on the durability and performance of your flooring system. Here are some key factors to consider when selecting a hangar epoxy flooring contractor:
- Experience and Expertise: Look for a contractor with extensive experience in installing epoxy flooring specifically for hangars. They should have a solid understanding of the unique requirements and challenges associated with hangar environments. An experienced contractor will have the knowledge and skills to ensure a successful installation.
- Portfolio and References: Ask the contractor for their portfolio of previous hangar epoxy flooring projects. This will give you an idea of the quality of their work and their ability to meet your specific needs. Additionally, request references from past clients to get feedback on their experience working with the contractor.
- Quality of Materials: Inquire about the type of epoxy materials the contractor uses. High-quality materials are essential for a durable and long-lasting flooring system. Ask about the brand and specifications of the materials to ensure they meet your hangar’s requirements.
- Certifications and Training: Check if the contractor has any certifications or training in epoxy flooring installation. Certifications from reputable organizations indicate that the contractor has undergone rigorous training and has met certain industry standards.
- Insurance and Warranty: Confirm that the contractor has liability insurance to protect against any damages that may occur during the installation process. Additionally, inquire about the warranty they offer for their workmanship and the epoxy materials. A reputable contractor will stand behind their work and offer a warranty to provide peace of mind.
- Communication and Collaboration: Effective communication is essential for a successful collaboration. Look for a contractor who is responsive, attentive to your needs, and willing to provide regular updates throughout the project. They should be able to address any concerns or questions you may have promptly.
- Cost and Timeline: While cost is an important consideration, it should not be the sole determining factor. Compare the quotes from different contractors, but also consider the quality of their work and the materials they use. Additionally, discuss the estimated timeline for the project to ensure it aligns with your schedule.
Epoxy Coating for my Hangar
Hangar Floor Coatings Epoxy For Concrete Epoxy Floor
Hangar Flooring Epoxy Flooring Installation for Airplane Hangars
Airplane Hangar Case Study Charlotte, NC – Liquid Floors, Inc
Airplane Hangar Floor Coating Specialized Epoxy u0026 Urethane Solutions
ArmorUltra 3 Gal Kit Epoxy 100% Solids
Airport Hangar Epoxy Floor Coating AES
Industrial and Hangar
Airplane Hangar Floor Coating Specialized Epoxy u0026 Urethane Solutions
Related Posts: