Acid Stain and Epoxy Coatings: What Sets Them Apart?
When it comes to garage floor finishes, two popular options are acid stain and epoxy coatings. While both can enhance the appearance and durability of your garage floor, they have distinct differences that make each suitable for different preferences and circumstances.
- Composition and Appearance: Acid stain penetrates the concrete surface, reacting chemically with the minerals to create a unique, mottled appearance. It produces a natural, variegated look with earthy tones like browns, reds, and greens. On the other hand, epoxy coatings are composed of resin and hardeners, providing a glossy, smooth finish. Epoxy floors come in a wide range of colors and can even incorporate decorative elements like flakes or metallic pigments.
- Durability and Maintenance: Acid stain offers excellent durability because it chemically bonds with the concrete, creating a permanent coloration that won’t chip or peel. However, it may require periodic resealing to maintain its appearance and protect against stains. Epoxy coatings are exceptionally durable, forming a tough, impermeable barrier that resists stains, abrasion, and chemicals. They are also easier to clean and maintain compared to acid-stained floors.
- Application Process: Acid staining involves a multi-step process that includes surface preparation, application of the acid stain, and neutralization followed by sealing. It requires skill and precision to achieve the desired color variation and finish. In contrast, epoxy coatings involve surface preparation to ensure adhesion, followed by the application of multiple layers of epoxy and a topcoat. While both processes require careful attention to detail, epoxy coatings typically have a shorter curing time.
- Cost Considerations: The cost of acid staining versus epoxy coatings can vary depending on factors such as the condition of the existing concrete, the complexity of the design, and labor costs. Generally, acid staining tends to be more cost-effective initially but may require more frequent maintenance over time. Epoxy coatings may have a higher upfront cost, but their long-term durability and low maintenance requirements can result in cost savings over the lifespan of the floor.
- Suitability for Different Environments: Acid stain is ideal for homeowners seeking a natural, rustic look for their garage floor. It’s particularly well-suited for residential spaces, workshops, and retail settings where aesthetics are a priority. Epoxy coatings, on the other hand, are versatile and suitable for a wide range of environments including garages, warehouses, commercial kitchens, and industrial facilities. They provide a seamless, non-porous surface that resists moisture, chemicals, and heavy foot traffic.
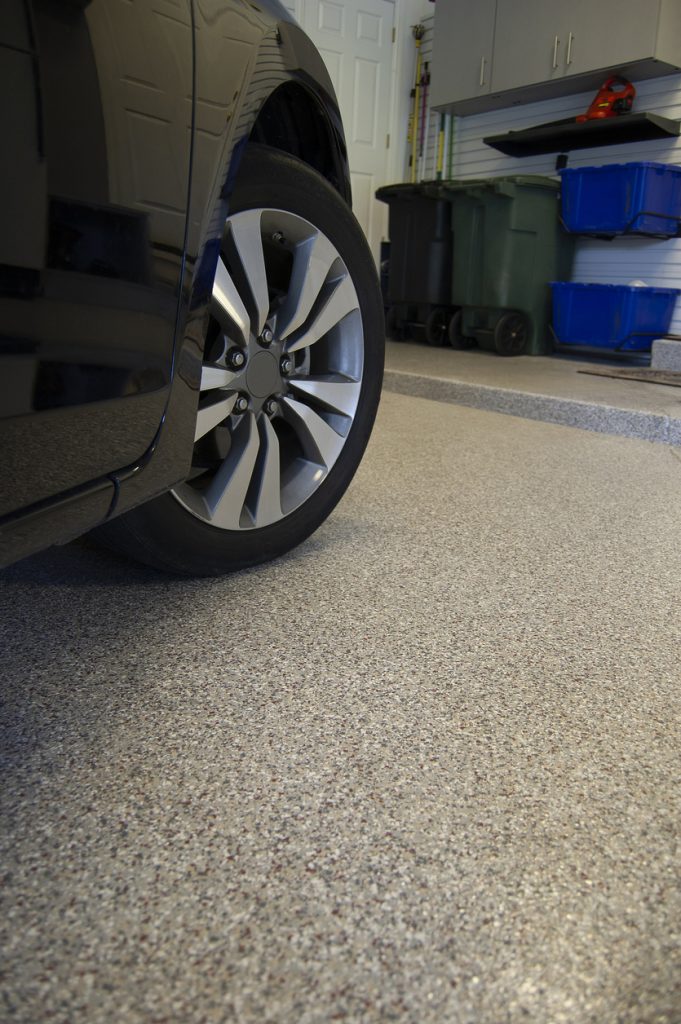
Pros and Cons of Acid Stain Garage Floors
Acid stain garage floors have gained popularity for their distinctive appearance and durability. However, like any flooring option, they come with their own set of advantages and disadvantages that homeowners should consider before making a decision.
Pros:
Unique Aesthetic: Acid stain creates a one-of-a-kind marbled effect that adds character and depth to your garage floor. The natural variations in color and texture can mimic the look of stone or marble, giving your space a high-end, custom finish.
Durability: Once properly applied and sealed, acid stain forms a permanent bond with the concrete, making it resistant to chipping, peeling, and fading. It can withstand heavy foot traffic, vehicle traffic, and exposure to chemicals without compromising its appearance.
Low Maintenance: Acid stain garage floors are relatively easy to maintain compared to other flooring options. Routine cleaning with a mild detergent and occasional resealing every few years can keep the floor looking fresh and vibrant for years to come.
Environmentally Friendly: Acid stain is made from natural, non-toxic ingredients, making it a sustainable choice for eco-conscious homeowners. It does not emit harmful fumes or VOCs (volatile organic compounds) during application or curing.
Cons:
Limited Color Options: While acid stain offers a range of earthy tones, the color palette is more limited compared to other flooring options like epoxy coatings. Achieving specific colors or intricate designs with acid stains can be challenging, as the final result is influenced by factors such as concrete composition and surface conditions.
Variable Results: The outcome of acid staining can be unpredictable, as it depends on factors such as concrete porosity, ambient temperature, and application technique. This variability can lead to inconsistencies in color and pattern, which may not always meet expectations.
Time-Consuming Application: Acid staining requires meticulous surface preparation and multiple application steps to achieve the desired results. It can be a time-consuming process, especially for larger areas or intricate designs, requiring patience and attention to detail.
Susceptibility to Damage: While acid stain is durable, it is not indestructible. Heavy impacts or abrasive materials can cause etching or scratching on the surface, detracting from its appearance. Additionally, prolonged exposure to harsh chemicals or UV radiation may cause fading or discoloration over time.
Exploring the Benefits and Drawbacks of Epoxy Garage Floors
Epoxy garage floors have become increasingly popular for their versatility, durability, and aesthetic appeal. However, like any flooring option, they have both advantages and disadvantages that homeowners should consider before installation.
Pros:
Exceptional Durability: Epoxy coatings form a seamless, non-porous surface that resists stains, abrasion, and impact damage. They can withstand heavy foot traffic, vehicle traffic, and exposure to chemicals without deteriorating or losing their luster.
Versatile Design Options: Epoxy coatings come in a wide range of colors, finishes, and textures, allowing homeowners to customize their garage floors to suit their preferences and style. Decorative elements like flakes, metallic pigments, and stenciled designs can be incorporated to create unique, eye-catching effects.
Easy to Clean and Maintain: Epoxy garage floors are incredibly low maintenance, requiring only routine sweeping and occasional mopping to keep them looking pristine. Unlike porous surfaces like concrete or tile, epoxy coatings repel dirt, oil, and other contaminants, making cleanup quick and effortless.
Resistant to Environmental Factors: Epoxy coatings are highly resistant to moisture, chemicals, UV radiation, and temperature fluctuations, making them suitable for a variety of climates and environments. They provide long-lasting protection against common sources of damage, such as water infiltration, oil spills, and corrosive substances.
Cons:
Labor-Intensive Installation: The installation process for epoxy garage floors can be complex and time-consuming, especially for DIY enthusiasts. It involves meticulous surface preparation, application of multiple epoxy layers, and proper curing to ensure optimal adhesion and durability.
Limited DIY Feasibility: While epoxy kits are available for DIY installation, achieving professional-quality results can be challenging without proper equipment, experience, and skill. Mistakes during application, such as improper mixing or uneven coating, can compromise the integrity and appearance of the floor.
Vulnerability to UV Damage: Epoxy coatings may yellow or discolor over time when exposed to direct sunlight, particularly in outdoor or partially covered garage environments. UV-stable formulations and topcoat sealants can help mitigate this issue, but periodic maintenance may be required to preserve the floor’s appearance.
Higher Upfront Cost: Compared to other garage flooring options, such as acid stain or paint, epoxy coatings typically have a higher initial cost due to materials, labor, and preparation expenses. However, many homeowners view this investment as worthwhile given the long-term durability and aesthetic benefits of epoxy garage floors.
Installation Process: Acid Stain vs. Epoxy Coatings
The installation process for acid stain and epoxy coatings differs significantly, each requiring specific techniques, materials, and considerations to achieve optimal results. Understanding the steps involved in both processes can help homeowners make informed decisions about which flooring option best suits their needs and preferences.
Acid Stain Installation Process:
Surface Preparation:
The first step in acid stain installation is thorough surface preparation to ensure proper adhesion and color penetration. This typically involves cleaning the concrete surface to remove dirt, oil, grease, and other contaminants using a degreaser or etching solution.
Any existing coatings or sealants must be removed to allow the acid stain to penetrate the concrete effectively. This may require mechanical grinding, shot blasting, or chemical stripping depending on the condition of the floor.
Application of Acid Stain:
Once the surface is clean and dry, the acid stain is applied using a sprayer, brush, or roller. The acid stain reacts chemically with the minerals in the concrete, creating a variegated, translucent effect that becomes permanent once the color develops.
Multiple coats of acid stain may be applied to achieve the desired depth of color and variation. It’s essential to work methodically and avoid overlaps or puddling to ensure uniform coverage and consistent results.
Neutralization and Sealing:
After the acid stain has fully reacted and dried, the surface is neutralized using a solution of baking soda and water to stop the chemical reaction and stabilize the pH. This step helps prevent residual acid from causing further damage to the concrete.
Once neutralized and thoroughly rinsed, the floor is sealed with a penetrating sealer to enhance color intensity, protect against stains and moisture, and provide a satin or gloss finish. Additional coats of sealer may be applied for added durability and shine.
Epoxy Coatings Installation Process:
Surface Preparation:
Similar to acid stain installation, surface preparation is critical for epoxy coatings to ensure proper adhesion and performance. This involves cleaning the concrete surface to remove dirt, oil, grease, and contaminants using a degreaser and mechanical scrubbing or pressure washing.
Any cracks, holes, or imperfections in the concrete are repaired using patching compounds or fillers, and the surface is roughened with a diamond grinder or shot blaster to promote adhesion.
Priming and Base Coat Application:
Once the surface is clean and dry, a primer is applied to the concrete to enhance adhesion and seal the substrate. The primer may be tinted to enhance color depth and coverage, depending on the desired aesthetic.
After the primer has cured, a base coat of epoxy is applied using a roller or squeegee to create a uniform, seamless foundation for subsequent layers. This base coat provides thickness and durability to the floor, filling in minor imperfections and creating a smooth surface.
Decorative Effects (Optional):
If desired, decorative elements such as colored flakes, metallic pigments, or stenciled designs can be added to the epoxy base coat while it’s still wet. These decorative effects can enhance the visual appeal of the floor and create a custom look to suit the homeowner’s preferences.
Once the decorative elements are applied, the epoxy is allowed to cure partially before excess flakes or pigments are removed, and a clear topcoat is applied to encapsulate and protect the design.
Topcoat Application:
The final step in epoxy coatings installation is the application of a clear topcoat to provide additional protection, durability, and gloss or satin finish. The topcoat seals the surface, enhances color intensity, and provides resistance to UV radiation, chemicals, and abrasion.
Multiple coats of topcoat may be applied depending on the desired level of protection and sheen. It’s essential to follow manufacturer recommendations for curing times and environmental conditions to ensure optimal results.
Choosing the Right Garage Floor Solution
Selecting the right garage floor solution is a crucial decision for homeowners, as it can significantly impact the functionality, aesthetics, and value of their property. With various options available, including acid stain and epoxy coatings, it’s essential to consider several factors to make an informed choice.
Intended Use and Traffic Patterns:
Consider how you plan to use your garage and the level of foot and vehicle traffic it will experience. If your garage serves as a workshop, storage space, or recreational area, durability and resistance to stains, chemicals, and abrasion are essential considerations. Epoxy coatings are particularly well-suited for high-traffic environments due to their exceptional durability and resistance to wear and tear.
Aesthetic Preferences:
Determine the aesthetic style you want to achieve for your garage floor, whether it’s a natural, rustic look with acid stain or a sleek, modern finish with epoxy coatings. Acid stain offers unique color variations and patterns that mimic the look of natural stone, while epoxy coatings provide a smooth, glossy surface that can be customized with a wide range of colors and decorative effects.
Maintenance Requirements:
Evaluate the maintenance needs and long-term upkeep associated with each flooring option. While acid stain requires periodic resealing to maintain their appearance and protect against stains, epoxy coatings are relatively low maintenance and easy to clean with routine sweeping and occasional mopping. Consider your lifestyle and willingness to invest time and effort into maintaining your garage floor.
Budget and Cost Considerations:
Determine your budget for garage floor installation, including materials, labor, and any additional services such as surface preparation or customization. While acid stain may offer a more cost-effective solution initially, epoxy coatings can provide long-term savings due to their durability, longevity, and low maintenance requirements. Factor in the upfront cost as well as potential future expenses for repairs or maintenance.
Climate and Environmental Factors:
Take into account the climate and environmental conditions in your area, as these can affect the performance and longevity of your garage floor. Acid stains may be susceptible to fading or discoloration over time when exposed to UV radiation, while epoxy coatings offer UV resistance and can withstand temperature fluctuations, moisture, and humidity. Choose a flooring option that is well-suited to your local climate and environmental conditions.
Concrete Floor Improvement: Paint, Stain, or Epoxy?
Stained Garage Concrete Floor Turned Man Cave Direct Colors
Stained concrete is very durable when applied by Elite Epoxy Floors
Concrete Stain, Epoxy, Garage Floor Painting ProTEK Painters Newton
Concrete Staining Or Epoxy Coating: Which Is Right For You?
Related Posts: